Beam Project & Materials Selection Continuation
- Frances
- Jun 9, 2018
- 5 min read
Updated: Jun 13, 2018
Our team project for school was to perform a beam trade study, sizing and selecting materials for three beams that could support a 15,000 lb load: one being the cheapest beam, one being the lightest beam, and one being an optimal beam that struck a balance between cost and weight.
How we solved this problem...
Given the following set parameters:
Applied force = 15000 lb
Chord & web length (l) = 36 in
Rivet diameter (d) >/= 1/32 in, </= 5/8 in
Took shear, bearing, and tensile failure modes into consideration
Used failure modes and dimensional constraints (spacing between rivets, chord thickness, beam thickness) to design either a 2-chord or 4-chord beam configuration
Down-selected materials for beam using:
Relevant mechanical properties
Bulk material costs
Machining costs
Chose best configuration and material for a cheap beam, a light beam, and a beam that struck a balance between cost and weight
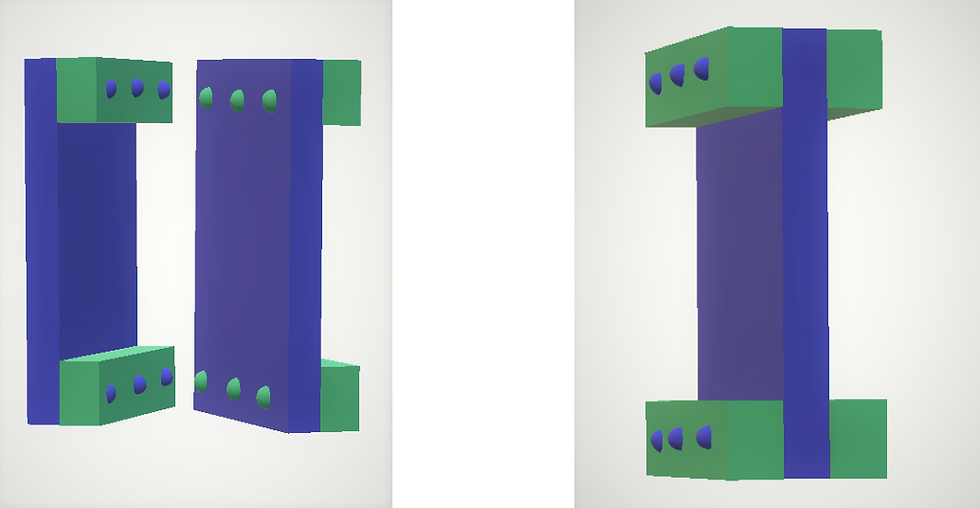
Figure 1. 2-chord beam configuration Figure 2. 4-chord beam configuration
Project Continuation (Independent)
After the project was finished, I was introduced to a useful materials selection software called CES Edupack, created by Granta Material Intelligence. Unfortunately, none of us on the team were aware of this software while we were working on the project, otherwise we could have used it for our materials down-selection process. Materials down-selection was something that we as a group didn’t get to do in a methodical manner due to time constraints, so to get familiar with CES Edupack and the down-selection process, I decided to do a down-selection process on my own.
Using the equation for shear stress, the applied force F = 15000 lb, and the upper and lower diameter bounds of ⅝ in and 1/32 in respectively, the allowable range of yield strength was 48,892.39 psi and 19.6 Mpsi, or 337 MPa to 135 GPa, which is a very wide range. Besides being able to fit within the given dimensional and loading parameters, wear and tear effects were also incorporated into the material selection.
In our problem statement, it was suggested that the cheapest beam could have applications most likely in civil engineering (ie. bridge), the lightest beam could have applications in aerospace engineering (ie. airplane), and the optimal beam could have applications in aerospace or automotive industries. Using logical reasoning and research on the important factors to consider for material selection for beams in the suggested application, more parameters were incorporated into the selection criteria.
1. Material Selection for Cheapest Beam: Structural Carbon Steel S275N (Steel A36)
Parameters:
High durability: excellent resistance to acids/bases, salt/fresh water, oxidation at 500 C, UV radiation, galling resistance (adhesive wear), and non-flammable characteristics
Non-brittle material: non-ceramic or glass
Non-magnetic
High melting point, >600 C
More applicable to aerospace applications, but was incorporated anyways to obtain the most durable material
Opaque
Price: <100 USD/kg
After inputting these parameters into the software, a graph plotting price in USD per kg versus the density in kg/m^3 of the materials that passed the selection criteria was made. From the graph (Figure 3), it was found that AISI 201 stainless steels were the cheapest materials that fit the criteria.

Figure 3: Price versus density of materials for the cheapest beam (1).
However, upon researching what materials were used commonly for structural beams, it was found that A36 structural carbon steel is what is commonly used (2). Upon comparison of the two using CES Edupack 2018, it was found that A36 structural carbon steels, like structural steel S275, had comparable mechanical property strengths, excellent durability under a few important environmental stresses like UV radiation and organic solvents (ie. gasoline leaking from a car), and acceptable durability under fresh water and several other environmental factors. Based on the fact that A36 structural carbon steel is very often used for applications like beams for bridges, it is likely that a high durability in harsh conditions is not as necessary for structural beams as initially predicted. In addition, A36 structural steel was found to some key favorable properties over 201 stainless steels for structural applications, which are underlined in Table 1.
Table 1: A36-Structural Carbon Steel S275N vs. Stainless Steel AISI 201

***Final Selection: Structural Carbon Steel S275N (Steel A36)***
_____
2. Material Selection for Lightest Beam: Carbon Fiber Reinforced Carbon Matrix Composite (Vf:40%)
Parameters:
High durability: excellent resistance to salt/fresh water; acceptable or excellent resistance to weak acids, weak alkalis, and organic solvents; fair, good, or excellent resistance to UV radiation, non-flammable characteristics
Non-brittle material: non-ceramic or glass
Non-magnetic
Very high melting point, >1000 C
Applicable to aerospace applications
Opaque
After inputting these parameters into the software, a graph plotting price in USD per kg versus the density in kg/m^3 of the materials that passed the selection criteria was made. From the graph (Figure 4), it was found that Carbon fiber reinforced carbon matrix composite (Vf: 40%) was the lightest material that fit the criteria.
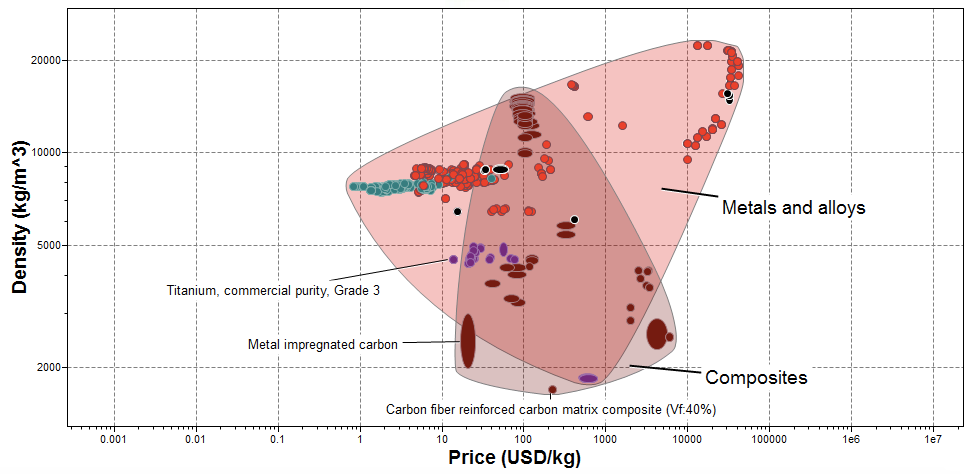
Figure 4: Price versus density of materials for the lightest beam (1).
Upon further research, it was found that composites like carbon fiber reinforced composites are indeed used for applications in aerospace (maybe not this specific material, but ones similar). Carbon fiber reinforced epoxies are one of the main three composites used in aerospace today, along with glass reinforced epoxy and aramid reinforced epoxy.
***Final Selection: Carbon fiber reinforced carbon matrix composite (Vf: 40%)***
_____
3. Material Selection for Optimal Beam: Titanium, commercial purity, Grade 1
Parameters:
High durability: excellent resistance to salt/fresh water; acceptable or excellent resistance to weak acids, weak alkalis, and organic solvents; fair, good, or excellent resistance to UV radiation, non-flammable characteristics
Excellent weldability
Non-brittle material: non-ceramic or glass
Non-magnetic
High melting point, >600 C
Opaque
Price: <100 USD/kg
After inputting these parameters into the software, a graph plotting price in USD per kg versus the density in kg/m^3 of the materials that passed the selection criteria was made. From the graph (Figure 5), it was found that Titanium, commercial purity, Grade 3 was the cheapest and lightest material that fit the criteria.
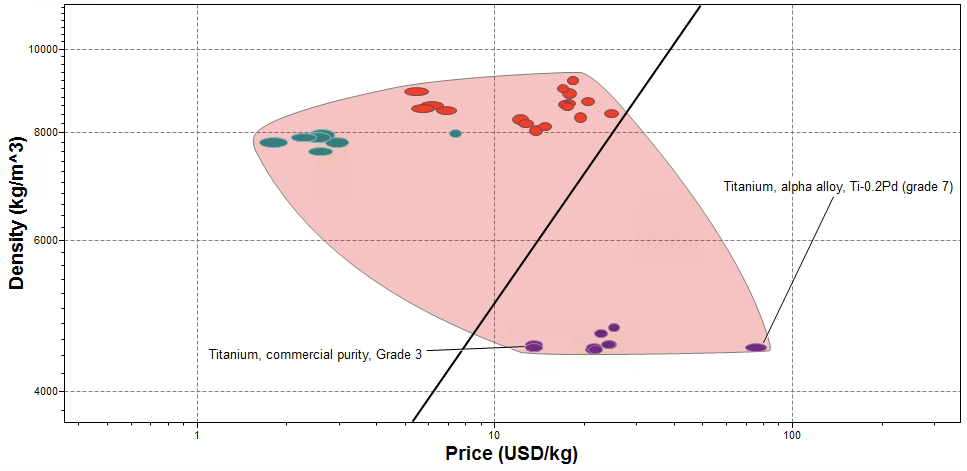
Figure 5: Price versus density of materials for the optimal beam (1).
An index line was added to separate the higher density materials (teal spots representing steels, red spots representing chromium alloys). Upon further research, it was found that Grade 3 titanium is indeed used for aerospace applications, although not as often as Grades 1 or 2. Grade 7 titanium was also considered, in case its properties were superior and relevant enough to the automotive/aerospace industries to outweigh the higher cost, but the alloy was found to be primarily used for chemical processes and production equipment components.
Grade 1 Titanium was compared to Grade 3 Titanium to determine which one was more ideal, according to a few more properties that were researched to be especially important for applications in automotive/aerospace industries (3). All property values were taken from CES Edupack 2018.
Table 2: Grade 1 Titanium vs. Grade 3 Titanium

Based on the comparison between the two, because of the higher fracture toughness and toughness (G) it was found that Grade 1 titanium is the optimal beam material.
***Final Selection: Titanium, commercial purity, Grade 1***
_____
Sources
CES Edupack Software, Granta Design. 2018
Manual of Steel Construction, 8th Edition, 2nd revised printing, American Institute of Steel Construction, 1987, ch 1 page 1-5
Motor Vehicle Assembly, EBRD Sub Sector Environmental & Social Guideline, 2014, page 14
コメント